可靠性高 焊膏 这些浆料可承受极端条件,确保电子元件长期稳固地结合在一起。然而,围绕这些浆料的讨论往往几乎都集中在其可靠性上,而忽略了同样重要的性能指标,如润湿性、无效性和可印刷性。
本文转换了视角,主张采用更全面的方法来开发和评估焊膏。在这一方法中,高可靠性与所有相关方面的卓越性能保持平衡。
返工和报废的实际成本
如果浆料在可靠性方面表现出色,但在其他方面却不尽如人意,就会导致返工率和废品率上升。其后果不仅是技术上的,也是经济上的。
返工校正 焊点不良、桥接或其他缺陷废品率 - 消耗宝贵的时间和资源,严重影响生产进度和运营效率。废品率是浪费材料的直接衡量标准,它进一步增加了成本。
返工和废品的真正成本还包括生产力损失、产品交付延迟,甚至声誉受损。在以下行业 航天, 汽车在医疗设备领域,可靠性至关重要。在这种情况下,如果达不到严格的质量标准,后果将不堪设想。这就强调了对在所有指标上都表现可靠的焊膏的需求。
为实际应用开发浆料
开发符合这些综合性能标准的焊膏需要严格的方法。这就是为什么我们拥有最先进的应用实验室来模拟真实的制造环境。这种亲身实践的实证方法确保了产品不仅在理论上站得住脚,而且在实践中行之有效。
通过这种方法,我们还可以对浆料配方进行微调。我们可以减少复杂装配中的空隙,提高在各种基材上的润湿性,并确保在各种工艺中都能保持一致的印刷适性。
AIM 的 REL22TM:全面表现案例研究
REL22TM 是一种高可靠性合金,可承受最极端的环境。其设计旨在兼顾最小空隙、优异的润湿性和出色的印刷适性,以及持久的机械强度和热回弹性。
REL22TM 与其他高可靠性合金不同的是,它具有为最苛刻的应用量身定制的一系列特性:
- 更广泛的 装配工艺窗口: REL22TM 具有多功能性,可适应更广泛的装配工艺和条件。
- 排尿次数明显减少 REL22TM 已证明可显著减少空洞,而空洞是提高电子组件寿命和可靠性的关键因素。
- 润湿更快更强 这种合金的成分可确保快速而稳定的润湿,这对形成牢固可靠的焊点至关重要。
- 增强拉伸强度: 无论是浇铸还是老化后,REL22TM 在长时间使用后,仍能保持坚固,并能承受机械应力。
- 降低蠕变率: 其配方经过优化,具有较低的蠕变率,这对于在热应力下保持连接完整性至关重要。
- 卓越的热循环性能: REL22TM 在热循环中表现出色,展示了其承受反复热偏移而不降低性能的能力。
虽然我们已经证明 REL22TM 除了在我们自己的实验室中多次验证该产品的性能外,该产品还通过了第三方测试的验证。这些额外的测试为我们的客户提供了信心,并确认该产品将满足他们的需求。DfR、奥本大学、Cree Lighting 和 Rockwell Collins 等机构都对 REL22 进行了比较研究。TM 和其他浆糊相比。
以下是此类测试的部分结果:
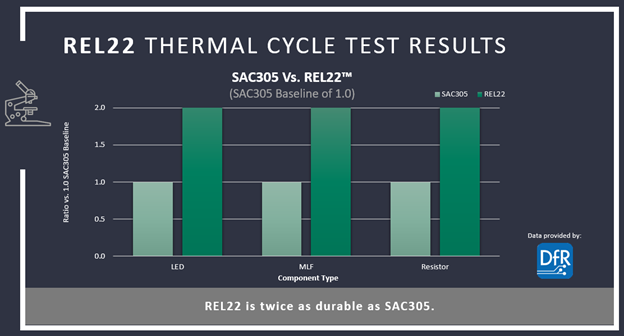
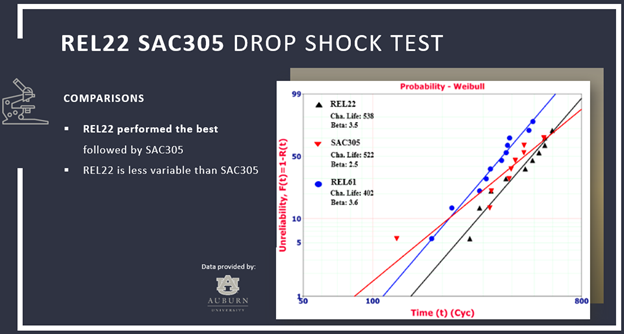
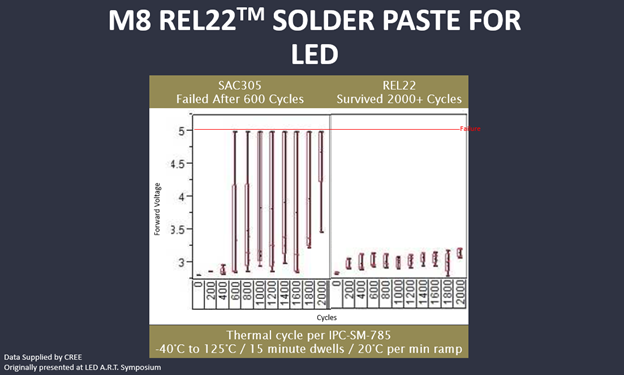
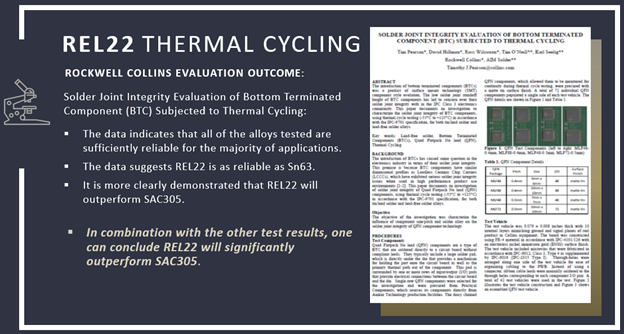
以下图片展示了 REL22TM与竞争对手的高可靠性浆料相比,该浆料的空泡性能更为出色。
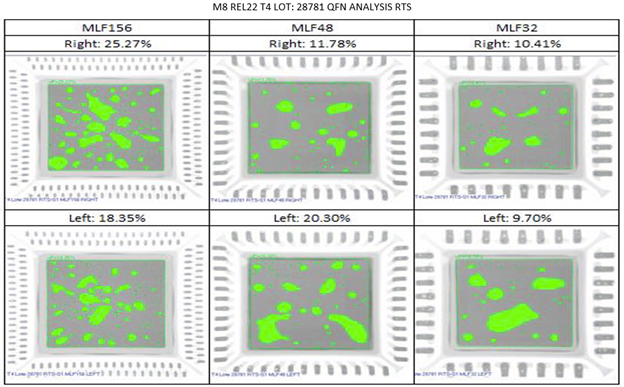
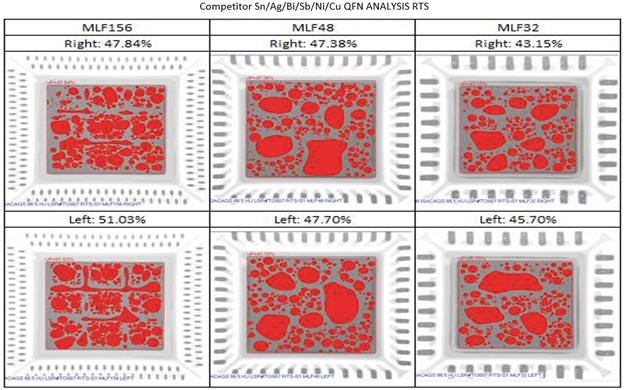
在热冲击测试中,REL22TM 其合格率为 98.53%,明显优于多个竞争对手的 SAC305 和高可靠性焊料,而竞争对手的合格率为 80.14-94.65%。
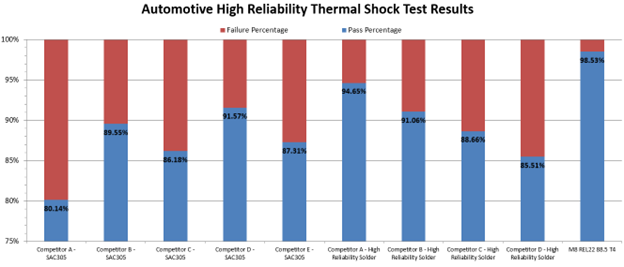
最后说明
可靠性只是性能的一个方面。现代电子制造要求材料不仅要能承受恶劣的条件,而且还要在不影响润湿、空洞、可印刷性和整体装配效率的前提下做到这一点。考虑到所涉及的经济和声誉问题,对锡膏性能采取综合方法并非奢望,而是必须的。
AIM Solder's REL22TM 不仅多次获得第三方测试人员和客户的认可,还获得了整个行业的认可。在 2018 年的 IPC APEX 大会上,它甚至获得了 Circuits Assembly 的新产品介绍(NPI)奖。
了解有关 REL22 的更多信息TM 以及 AIM Solder 对创新和质量的承诺如何支持您的制造目标。让我们一起重新定义焊接行业的 "高可靠性"。