RÉSUMÉ
Alors que l'industrie électronique s'efforce continuellement d'innover et d'améliorer l'efficacité des processus d'assemblage et de retouche, l'exploration des alliages de soudure à basse température (LT) a fait l'objet d'une attention particulière. Cet article fournit une analyse complète de la soudure à basse température, en se concentrant particulièrement sur son application dans les processus de reprise et sur les implications plus larges pour la fabrication électronique. Nous nous penchons sur les différentes facettes de la soudure à basse température, en examinant à la fois les avantages potentiels et les défis associés à son utilisation.
L'étude revisite les travaux antérieurs sur la soudure à basse température dans les travaux de reprise, offrant un résumé détaillé et suggérant une approche prudente en raison des coûts accrus et des complexités associées au fil de soudure contenant du bismuth, ainsi que de l'absence de différences substantielles dans la solidité et la fiabilité des joints par rapport aux méthodes traditionnelles. En outre, le document aborde des considérations plus générales sur la soudure à basse température, notamment les avantages et les inconvénients, les compromis en matière de performances et les domaines nécessitant des études plus approfondies.
Cette étude sur la soudure à basse température est enrichie par de nouvelles données sur le nettoyage des résidus d'oxyde de bismuth et sur les effets de la température de la pointe et du temps de contact sur la formation d'IMC pendant la reprise. En fournissant une vue d'ensemble complète des recherches existantes et des nouveaux résultats, cet article vise à offrir des informations précieuses aux fabricants, aux ingénieurs et aux chercheurs, contribuant ainsi à des décisions éclairées concernant l'adoption et l'intégration de la soudure à basse température dans le retraitement et l'assemblage de l'électronique.
INTRODUCTION
À une époque où l'innovation et l'efficacité sont devenues primordiales, l'industrie de la fabrication électronique cherche constamment des moyens d'améliorer les processus, de réduire les coûts et d'accroître la fiabilité des produits. Parmi les diverses solutions explorées, la soudure à basse température (LT) est apparue comme une alternative prometteuse aux méthodes de soudure traditionnelles, en particulier avec la prolifération de produits électroniques complexes et miniaturisés.
Historiquement, l'utilisation de la soudure LT a été motivée par ses caractéristiques uniques, telles qu'un point de fusion réduit et la possibilité d'économiser de l'énergie et des matériaux.[1]
Cependant, comme pour tout changement significatif de méthodologie, la mise en œuvre de la soudure à basse température a engendré son lot de défis. Ces défis, qui vont de la fiabilité à la gestion des résidus en passant par les problèmes de retouche, nécessitent une exploration et une compréhension plus approfondies.
Cet article se penche sur les subtilités de la soudure à basse température, en particulier dans le domaine de la retouche et de l'assemblage des composants électroniques. Grâce à un examen rigoureux et à une combinaison de données expérimentales et de points de vue industriels, nous visons à mettre en lumière le véritable potentiel, les avantages et les considérations liés à l'utilisation de la soudure à LT dans la fabrication électronique contemporaine.
CONTEXTE
Les informations sur les caractéristiques et les problèmes clés liés au brasage à LT sont souvent disparates, les études en cours et existantes étant embourbées par des différences de méthodologies, par l'enchevêtrement avec les efforts de marketing et par le manque de conclusions méta-analytiques suffisamment solides pour fournir des informations directes et exploitables aux fabricants. Le présent document vise à entamer le processus de regroupement des informations existantes en une image cohérente, en identifiant à la fois les avantages et les défis associés au brasage tendre dans différentes dimensions, tout en délimitant clairement les questions et les domaines d'étude restants, ainsi que les conclusions normalisées des travaux existants.
Alliages à basse température
Les soudures LT se caractérisent par leur composition métallique unique, principalement à base d'étain (Sn) et de bismuth (Bi). Historiquement, la présence de plomb (Pb) dans les soudures était courante, mais avec l'évolution vers des processus sans plomb, le bismuth est devenu un composant plus viable.[2] La prédominance de l'étain et du bismuth dans ces alliages marque un changement important dans la technologie des soudures. Le bismuth, auparavant négligé en raison de son incompatibilité avec les procédés à base de Pb, fait désormais partie intégrante des brasures LT, d'autant plus que la plupart des procédés de brasage sont désormais exempts de Pb. Cette transition a stimulé le développement de nouvelles générations de brasures LT. Bien qu'il existe une variété croissante de compositions de brasage à LT, cet article se concentrera principalement sur l'étain-bismuth eutectique et l'étain-bismuth avec un léger ajout d'argent (Ag), car ces compositions représentent une part importante des applications actuelles de brasage à LT.
Principaux avantages et inconvénients de la soudure LT
Les principaux avantages de la soudure LT résident dans ses températures de fusion plus basses que celles des soudures traditionnelles. Cette caractéristique présente plusieurs avantages. Le premier est la réduction de la consommation d'énergie. Le point de fusion plus bas permet d'économiser de l'énergie pendant le processus de brasage, car moins de chaleur est nécessaire. En fait, certaines études ont montré des économies d'énergie potentielles allant jusqu'à 20-40% en utilisant des profils de refusion à basse température par rapport à ceux de la SAC305 traditionnelle.[3]
Un autre avantage est la diminution du gauchissement des composants. Des températures plus basses réduisent le risque de déformation des composants sensibles pendant la soudure, améliorant ainsi l'intégrité du produit.
Toutefois, ces avantages sont contrebalancés par certains inconvénients. Notamment, le bismuth, bien qu'avantageux pour abaisser le point de fusion, introduit une fragilité dans les joints de soudure. Cela peut affecter la fiabilité et la durabilité des connexions soudées, en particulier dans les environnements où les contraintes mécaniques sont un problème.
Un autre inconvénient est lié à la sensibilité à la température. Si des températures plus basses sont bénéfiques pour les économies d'énergie et la réduction du gauchissement, elles nécessitent également un contrôle et un étalonnage minutieux pendant le processus de brasage afin de garantir l'intégrité du joint.
Des questions se posent également sur la création de joints hybrides (souvent SAC+LT) dans divers scénarios et sur les caractéristiques et les modes de défaillance de ces joints.[4] C'est une question que nous avons déjà étudiée dans le cas des travaux de reprise utilisant des soudures à basse température. Les changements de processus constituent un autre domaine d'exploration, comme l'ajustement des taux de rampe et l'utilisation de fours de refusion avec des zones de refroidissement. [5][6]
Reprise de soudure à basse température
L'une des questions que se posent de nombreux fabricants lorsqu'ils mettent en œuvre des procédés de brasage à basse température est de savoir s'ils peuvent ou doivent également utiliser de la brasure à basse température dans les travaux de retouche effectués sur les composants qui ont été brasés avec de la brasure à basse température. Cette question est double : premièrement, si la soudure LT dans le processus nécessite une soudure LT dans la retouche pour maintenir l'intégrité du joint, et deuxièmement, si l'utilisation de la soudure LT dans la retouche apporte des avantages supplémentaires et des économies, de la même manière que la soudure LT utilisée dans la refusion et le soudage à la vague.
La discussion vise à fournir une compréhension complète du rôle de la soudure LT dans la reprise, en mettant en évidence les considérations clés pour les fabricants qui envisagent de l'adopter dans leurs protocoles de réparation et d'entretien.
Résumé de l'étude précédente
L'étude initiale a exploré la viabilité des alliages LT dans les scénarios de reprise.[7] Il a été observé que le fil solide à basse température de fusion et le flux externe, ainsi que la brasure à fil SAC305 enrobée de flux, pouvaient être utilisés avec succès pour retravailler les alliages LT. La brasure LT présentait des caractéristiques de traitement distinctes de celles de la brasure SAC, mais celles-ci n'empêchaient pas la formation de joints de brasure de qualité.
Il est essentiel de noter que les joints brasés créés avec la brasure LT répondent aux critères IPC des classes 1, 2 et 3, ce qui suggère que la brasure LT est une option viable pour toute une série de classes de produits. Toutefois, les résultats des essais de cisaillement étaient variables, reflétant les défis inhérents aux processus de reprise. Les joints de soudure SAC ont démontré une plus grande ductilité par rapport à leurs homologues bismuthés, ce qui correspond aux propriétés matérielles connues de ces alliages. Lorsque la brasure à fil fourré SAC305 a été utilisée, le processus a ressemblé aux méthodes traditionnelles de reprise SAC/SAC, en mettant l'accent sur l'utilisation de diamètres de fil plus fins pour les composants plus petits.
L'étude a mis en évidence l'importance des compétences de l'opérateur, soulignant la nécessité d'une formation adéquate lors de la mise en œuvre de la reprise à LT. Ce point est particulièrement important étant donné la nature variable des résultats de la reprise, même sous la direction d'un opérateur très expérimenté.
Questions non résolues de l'étude initiale
Plusieurs questions sont restées en suspens et méritent d'être approfondies. L'une des principales questions non résolues est la nettoyabilité des résidus d'oxyde de bismuth après refusion et reprise. Cet aspect est crucial pour garantir la fiabilité et les performances à long terme des joints soudés.
L'étude originale indiquait également que les variables des techniques de brasage manuel, en particulier la température de la panne et le temps de contact, ont un impact significatif sur la formation de composés intermétalliques (IMC). Il est essentiel de comprendre ces variables pour optimiser les processus de reprise et garantir l'intégrité des joints de soudure.
Ces questions non résolues ont été étudiées comme décrit dans les deux sections suivantes.
Nettoyage des résidus d'oxyde de bismuth
L'une des principales préoccupations liées à l'utilisation de la soudure LT est la possibilité que des résidus d'oxyde de bismuth subsistent après les processus de refusion et de retouche. La présence de ce résidu peut avoir un impact sur la qualité et la fiabilité du joint de soudure, bien qu'il soit principalement considéré comme cosmétique. Une étude a été réalisée en partenariat avec MicroCare pour déterminer si ce résidu pouvait être nettoyé et quelle était la chimie de nettoyage la plus efficace.
Objectif de l'expérience
L'étude visait à évaluer l'efficacité de divers produits chimiques de nettoyage pour éliminer les résidus des joints de soudure créés à l'aide de soudure à basse température (LT). Cette étude était particulièrement axée sur l'évaluation de la capacité des différents agents de nettoyage à nettoyer les résidus d'oxyde de bismuth résultant des processus de brasage à basse température.
Matériaux utilisés
Dans cette étude, différents matériaux de soudure ont été utilisés. La sélection comprenait la pâte AIM M8 SAC305, la pâte NC273LT Sn42/Bi57/Ag1, le fil fourré SAC305 et le Sn42/Bi57/Ag1 solide en combinaison avec le flux NC280 (pour les composants PTH) ou NC217 (pour les composants SMT).
Pour évaluer le processus de nettoyage, trois produits chimiques distincts ont été envisagés. Deux d'entre elles étaient des nettoyants fluorés, appelés nettoyants X et Y, tandis que la troisième était un nettoyant non fluoré appelé nettoyant Z.
Dispositif expérimental et procédure
Pour la phase d'assemblage et d'essai, des coupons d'essai (PCB016) ont été créés pour chaque nettoyant examiné. Le processus d'assemblage a comporté plusieurs étapes. Les coupons A et B ont été refondus avec de la soudure LT et retravaillés avec du fil LT et un flux externe. Le coupon C a été refondu avec de la brasure LT et retravaillé avec du fil SAC305 fourré. Le coupon D a été refondu et retravaillé avec du fil SAC305. Enfin, le coupon E a été refondu avec de la brasure LT et n'a subi aucune retouche. L'étape initiale de cette phase a consisté à prendre des photos "avant" de tous les composants.
La procédure de nettoyage de la paillasse qui a suivi a consisté à appliquer un solvant de nettoyage à l'aide d'un outil de distribution. Le processus comprenait un cycle de nettoyage humide et de séchage, consistant en un nettoyage humide de 20 secondes, un nettoyage de 20 secondes et une période de séchage de 30 à 60 secondes. La propreté des coupons a ensuite été méticuleusement analysée au microscope, puis des photos "après" ont été prises.
Résultats
Après une expérimentation approfondie, le nettoyant X s'est avéré être le plus efficace pour les échantillons considérés. L'efficacité du nettoyage a été évaluée de manière plus approfondie en examinant des coupons d'essai spécifiques. Les coupons d'essai B, C et E ont présenté les résultats de nettoyage les plus satisfaisants avec le nettoyant X, indiquant une élimination réussie des résidus avec LT+LT, LT+SAC et LT sans retouche, respectivement (voir figure 1). Cependant, le coupon A (LT+LT) présentait de légers résidus à certains endroits, contrairement à son jumeau, le coupon B. Le coupon D (SAC+SAC) présentait plusieurs zones de résidus visibles après le nettoyage, comme l'illustrent les figures 2 et 3.
Figure 1. Composants du coupon d'essai C avant (à gauche) et après (à droite) le nettoyage avec le nettoyant X
Figure 2. Coupon d'essai A avant (à gauche) et après (à droite) le nettoyage avec le Cleaner X
Figure 3. Coupon d'essai D avant (à gauche) et après (à droite) le nettoyage avec le Cleaner X
Conclusion
L'étude a conclu que si le processus de nettoyage à l'aide du Cleaner X était efficace pour la plupart des coupons d'essai, l'élimination des résidus variait considérablement d'un échantillon à l'autre. L'étude souligne l'importance de sélectionner le produit chimique de nettoyage approprié et de suivre rigoureusement la procédure de nettoyage pour garantir une élimination efficace des résidus.
Considérations sur la croissance de l'IMC et variables dans les techniques de brasage manuel
La croissance des composés intermétalliques (IMC) est un facteur crucial dans l'évaluation de la fiabilité des joints de soudure. L'étude initiale avait montré des résultats comparables entre diverses combinaisons de brasage en termes d'essais de cisaillement et d'épaisseur de l'IMC. Toutefois, le taux de croissance de l'IMC et l'importance du temps de séjour dans cette formation font toujours l'objet d'un examen approfondi. L'élucidation de la dynamique de la croissance de l'IMC dans le contexte de la soudure LT peut apporter plus de clarté sur la viabilité à long terme de la soudure.
Effets de la variation du brasage manuel sur l'IMC et d'autres caractéristiques
Cette étude a été lancée pour répondre à la deuxième question de suivi de l'article initial sur les travaux de reprise à basse température.[7] Metcal, une société spécialisée dans la fabrication d'équipements de brasage manuel, a étudié l'impact de la température de la pointe et du temps de contact sur la formation de composés intermétalliques (IMC) et d'autres caractéristiques lors de l'utilisation de la soudure à basse température (LTS).
Matériaux utilisés
L'étude a utilisé l'alliage Sn42/Bi57/Ag1 pour la refusion et la reprise, le flux AIM NC280 étant utilisé avec le fil. Les composants soudés étaient cinq composants PTH (Plated-Through-Hole), comprenant trois résistances et deux condensateurs, sur un seul modèle de PCB. Le brasage manuel a été réalisé avec un fer à souder CVC-6CH0025S à pointe biseautée de 2,5 mm.
Dispositif expérimental et procédure
Les conditions de brasage ont été modifiées dans cette expérience, impliquant deux températures de pointe différentes, à savoir 285°C et 343°C, avec des ajustements correspondants des temps de contact. Plus précisément, pour 285°C, les temps de contact ont été fixés à 3s, 4s (ligne de base), 5s et 6s. En revanche, à 343°C, les temps de contact étaient de 2s (base), 3s, 4s et 5s.
Les paramètres d'évaluation se sont concentrés sur une analyse complète de divers aspects, notamment les joints de soudure, les caractéristiques des résidus, les propriétés de mouillage, la corrosion, la forme du joint de soudure, la confirmation du remplissage du tonneau, l'épaisseur de l'IMC et la présence de vides.
Résultats
Lors de l'examen des joints de soudure, il a été observé que certains joints présentaient un angle de contact supérieur à 90° à 285°C, particulièrement remarquable à un temps de contact de 3 secondes. Inversement, à 343°C, certains joints présentaient un excès de soudure sur la face supérieure, comme le montre la figure 4.
Figure 4. Angle de contact de la broche du condensateur après retouche à 285°C, temps de contact de 3 secondes
En ce qui concerne les résidus, la couleur s'est assombrie en corrélation avec le temps de contact pour les deux températures de pointe, comme le montre la figure 5.
Figure 5. Résidu de la face inférieure des composants retravaillés à 343°C
Les propriétés de mouillage de la soudure étaient remarquables, présentant un aspect brillant et lisse et assurant une bonne couverture de la surface de la pastille dans la majorité des joints.
Aucun cas de corrosion n'a été détecté dans les PCB analysés.
La forme des joints de soudure a été influencée par les conditions de température. Les composants soumis à 343°C ont formé de meilleurs joints de soudure sur différents temps de contact par rapport à ceux soumis à 285°C. Tous les fûts, à l'exception de la résistance avec 3 et 4 secondes de temps de contact à 285°C, ont été remplis à 100%.
L'étude de l'épaisseur de l'IMC a révélé qu'à 343°C, l'IMC PCB/Solder était plus élevé que l'IMC Pin/Solder. L'épaisseur de l'IMC était plus importante pour les composants dont le temps de contact était de 3 et 4 secondes que pour ceux dont le temps de contact était de 2 et 5 secondes. À 285 °C, l'IMC broche/soudure était plus élevé que l'IMC PCB/soudure, en particulier pour les résistances avec des temps de contact de 6 et 5 secondes. Les condensateurs à 285°C n'ont pas montré d'IMC Pin/Solder mesurable, suggérant qu'il était inférieur à 1µm. Voir la figure 6, le tableau 1 et le tableau 2 pour des informations détaillées.
Figure 6. Épaisseur de l'IMC après reprise de la broche de la résistance à 343°C, temps de contact de 4 secondes
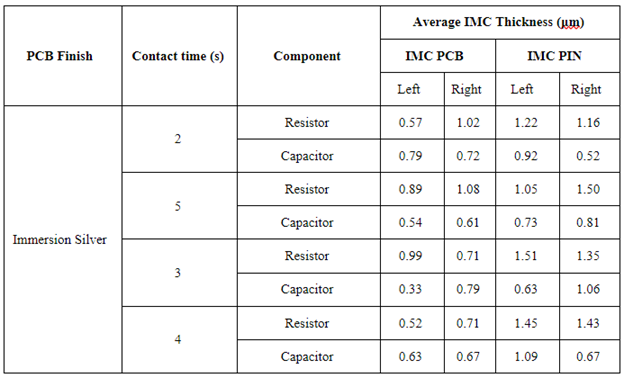
Tableau 1. Épaisseur moyenne de l'IMC 343°C
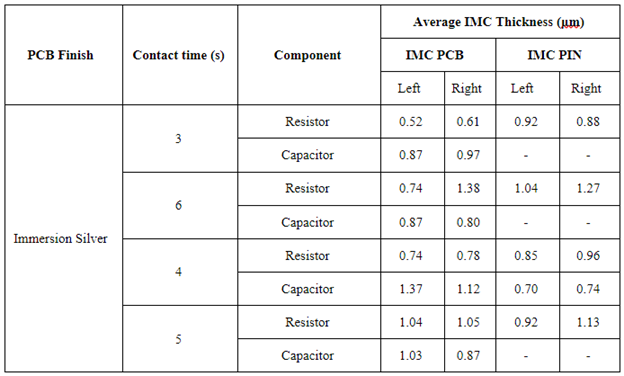
Tableau 2. Épaisseur moyenne de l'IMC 285°C
Enfin, la présence de vides a été une observation courante, plus de 80% des broches présentant des vides pour les deux températures et pour différents temps de contact.
Conclusions
Les résultats indiquent que des températures et des temps de contact différents influencent la qualité du joint de soudure et la formation d'IMC. La réponse à la question de savoir si l'utilisation de la soudure à basse température dans les travaux de reprise pourrait prolonger la durée de vie de la panne ou permettre d'économiser de l'énergie semble être négative. Dans l'ensemble, la température la plus élevée, 343°C, a donné les meilleurs résultats, 3 à 4 secondes étant le temps de contact idéal.
Autres considérations sur la croissance des IMC
Différentes approches de reprise, telles que LT+LT, LT+SAC et SAC+SAC, peuvent influencer la formation d'IMC de manière unique. Alors que les fabricants envisagent d'adopter la soudure LT pour la reprise, il est impératif de comprendre ces différences subtiles et leurs implications potentielles. De nombreuses études récentes ont examiné la croissance de l'IMC ainsi que la migration du bismuth dans les BGA, en comparant les effets de la LT+LT, de la LT+SAC et de la SAC+SAC.[8] Toutefois, les résultats d'une étude à l'autre ne révèlent pas de tendance précise. Il est également prouvé que la rampe de température, les vitesses de refroidissement et les temps de séjour peuvent avoir un impact significatif sur l'intégrité du joint lorsqu'il s'agit de soudures à basse température, qu'elles fassent ou non partie d'un joint hybride, comme nous l'avons mentionné précédemment. Cela semble indiquer la possibilité d'une plus grande variation des résultats du brasage manuel, en fonction des réglages de l'équipement et de l'expérience de l'opérateur.
Présentation des arguments en faveur de la soudure à basse température dans les travaux de reprise
Plusieurs facteurs clés doivent être pris en compte lors de l'examen des avantages potentiels de l'utilisation de la soudure à basse température (LT) dans les processus de reprise. Nos études et nos recherches ont permis de mieux comprendre chacun de ces aspects et de mieux cerner l'aspect pratique et l'efficacité de la soudure à basse température dans les scénarios de retouche.
Économies sur le coût des matériaux de soudure
Contrairement aux attentes en matière de rentabilité, le fil de soudure LT est nettement plus cher que le SAC305. Cela s'explique par le fait qu'un composant clé de la brasure LT, le bismuth, n'est pas très ductile, ce qui rend la fabrication du fil de brasure LT intrinsèquement plus difficile. Ce coût plus élevé compromet l'un des avantages potentiels de l'utilisation de la brasure LT dans les processus de reprise, ce qui en fait une option moins attrayante d'un point de vue financier.
Facilité d'utilisation
La facilité d'utilisation est un autre domaine dans lequel la soudure LT n'offre pas nécessairement d'avantages. L'exigence d'un fil non fourré et d'un flux externe complique le processus de reprise. En outre, elle exige un niveau plus élevé d'expertise et de précision de la part de l'opérateur. Ces facteurs contribuent à rendre le processus de reprise plus difficile et plus complexe.
Économies d'énergie
Alors que la soudure LT fond à des températures plus basses, ce qui suggère des économies d'énergie potentielles, nos résultats indiquent que l'intégrité du joint et la formation d'IMC sont améliorées lorsque l'on utilise une température de pointe plus chaude et un temps de contact modéré. Cela signifie qu'il n'y a pas d'économies d'énergie à réaliser lors de la reprise sans compromettre l'intégrité de l'ouvrage.
La vie en pointillés
Bien qu'il existe une possibilité théorique de prolonger la durée de vie de la pointe grâce à des températures de fonctionnement plus basses, nos recherches suggèrent à nouveau que cela ne se vérifie pas en raison des meilleurs résultats obtenus lors du brasage à une température plus élevée.
Intégrité de l'articulation
Notre étude initiale a comparé les performances des configurations SAC+SAC, LT+SAC et LT+LT en termes d'essais de cisaillement et d'épaisseur de l'IMC. Les résultats ont montré que toutes ces combinaisons étaient comparables en termes de performances. Cependant, des questions subsistent quant au taux de croissance de l'IMC et au temps de séjour, qui nécessitent des recherches plus approfondies pour comprendre pleinement les implications sur l'intégrité du joint.
Exigences en matière de température des composants/substrats
Une considération importante dans l'utilisation de la soudure à basse température est son impact sur le composant et le substrat. Si l'adoption de la soudure à basse température dans les processus de refusion conduit à l'utilisation de substrats et de composants moins chers, ceux-ci peuvent présenter des sensibilités spécifiques à la température lors de la refonte, qui doivent être gérées avec soin. Cet aspect de l'utilisation de la soudure à basse température nécessite une compréhension nuancée des matériaux concernés et de leurs tolérances de température respectives.
Nettoyage des résidus
Les soudures contenant du bismuth peuvent laisser des résidus d'oxyde de bismuth, à la fois après la refusion et après la retouche. En fait, une grande partie de ces résidus a été observée sur les composants retravaillés dans l'étude variable sur le fer à souder. Il a toutefois été établi qu'il existe une solution et un processus de nettoyage qui éliminent pratiquement ce résidu.
Conclusion
D'après les résultats cumulés de nos recherches et études, les arguments en faveur de l'utilisation de la soudure à basse température dans les processus de reprise ne sont pas très convaincants. Bien qu'il existe des avantages théoriques, les réalités pratiques et les résultats de nos enquêtes suggèrent que les avantages sont soit minimes, soit annulés par d'autres défis. Les fabricants doivent peser soigneusement ces facteurs lorsqu'ils envisagent d'adopter la soudure à basse température à des fins de reprise.
Cas d'utilisation primaire de la soudure à basse température
Enfin, nous aimerions réévaluer le champ d'application plus large des soudures à basse température (LT), en tenant compte à la fois de leurs limites inhérentes et des domaines dans lesquels elles sont prometteuses.
Rappelons que les brasures LT présentent une fiabilité moindre dans les scénarios impliquant des contraintes mécaniques, telles que les chocs de chute, où la fragilité peut constituer un obstacle important. Toutefois, elles peuvent être bien adaptées à l'électronique consommable où une durabilité élevée est moins critique et où il est essentiel de maintenir les coûts de fabrication à un niveau bas pour préserver la rentabilité.
Environnements d'application contrôlés
Dans les cas où le dispositif ne devrait pas subir de contraintes mécaniques importantes, comme dans les environnements stationnaires ou contrôlés, la fragilité de la soudure étain-bismuth peut ne pas être un problème majeur.
Combinaison avec d'autres alliages
Parfois, la soudure étain-bismuth peut être combinée avec d'autres alliages pour atténuer sa fragilité. Par exemple, l'ajout d'argent (Ag) peut améliorer sa résistance mécanique, ce qui la rend plus adaptée aux applications nécessitant un certain niveau de résistance aux chocs.
Composants redondants ou non critiques
Dans certaines conceptions, en particulier dans l'automobile et l'aérospatiale, la soudure étain-bismuth peut être utilisée pour les composants redondants ou non essentiels à la fonction principale du système, réduisant ainsi le risque associé à la défaillance des joints de soudure.
Électronique flexible
Dans le domaine de l'électronique flexible, l'accent est souvent mis sur la flexibilité plutôt que sur la résistance aux chocs mécaniques. Dans ce cas, la basse température de la soudure étain-bismuth est bénéfique pour les matériaux sensibles à la température utilisés dans ces appareils. Les appareils eux-mêmes peuvent être conçus pour subir un impact ou un choc minimal.
Utilisation dans les composants protégés
Dans les applications automobiles et aérospatiales, les composants soudés à l'étain-bismuth peuvent être logés dans des zones mécaniquement protégées où la probabilité de subir des chocs dus à des chutes est minimisée.
Application sélective
La soudure étain-bismuth peut être utilisée de manière sélective en association avec d'autres types de soudure dans un même assemblage, uniquement dans des domaines spécifiques où son faible point de fusion est avantageux et où sa fragilité n'est pas un inconvénient majeur.
Techniques d'emballage avancées
Certaines techniques modernes d'emballage électronique peuvent atténuer les effets de la fragilité de la soudure, comme l'utilisation de matériaux de remplissage ou l'emploi de circuits imprimés spécifiques qui réduisent la tension sur les joints de soudure.
Pièces non mobiles
Dans les secteurs de l'automobile et de l'aérospatiale, il peut être utilisé pour des pièces non mobiles ou dans des applications où les joints de soudure ne sont pas soumis à des contraintes mécaniques fréquentes ou sévères.
Pleins feux sur l'électronique consommable
Le segment des produits électroniques consommables est particulièrement intéressant si l'on considère l'adoption de la soudure à basse température. Il s'agit de produits souvent conçus dans l'optique d'un cycle de vie court, qu'il s'agisse d'accessoires pour téléphones portables ou d'écouteurs bon marché. Il convient de noter que si les appareils jetables utilisant la soudure à LT peuvent annuler les avantages environnementaux de l'utilisation de la soudure à LT en contribuant à l'excès de déchets, sur des marchés spécifiques où les appareils électroniques doivent être jetables (comme certaines applications médicales ou de sécurité), la soudure à LT peut contribuer à maintenir le rapport coût/efficacité.
Orientations futures et recommandations
L'exploration de la soudure à basse température (LT), son application dans la retouche et ses implications plus larges pour l'industrie électronique ont indubitablement permis d'accumuler une grande quantité de connaissances. Toutefois, comme dans toute entreprise scientifique, le voyage a permis de découvrir autant de questions qu'il n'a apporté de réponses. Sur la base des informations recueillies jusqu'à présent, plusieurs orientations et recommandations futures se dégagent.
Développement et normalisation des alliages
Dans une étude iNEMI, les personnes interrogées ont indiqué qu'elles souhaitaient qu'il y ait un alliage standard en LT avant d'investir dans le passage au numérique.[9] Comme nous l'avons vu plus haut, si l'étain-bismuth eutectique est le modèle "de base" auquel les alliages de LT plus sophistiqués sont souvent comparés ou modifiés pour résoudre les problèmes existants, l'ajout de dopants et d'autres éléments fait encore l'objet de nombreuses expérimentations.
L'amélioration de la fiabilité des soudures étain-bismuth (Sn-Bi) à basse température implique souvent l'ajout d'autres éléments à l'alliage. Ces ajouts sont destinés à améliorer certaines propriétés telles que la résistance mécanique, la performance des cycles thermiques et la réduction de la fragilité. Parmi les éléments les plus efficaces à cette fin, citons :
- Argent (Ag): L'ajout d'argent aux alliages Sn-Bi est l'une des méthodes les plus courantes pour améliorer leur résistance mécanique et leur résistance à la fatigue thermique. L'argent peut améliorer la robustesse globale du joint de soudure, le rendant moins sujet aux défaillances sous l'effet des contraintes mécaniques ou des cycles thermiques.
- Cuivre (Cu): Le cuivre est un autre élément souvent ajouté aux soudures Sn-Bi. Il peut améliorer les caractéristiques de mouillage de la soudure et renforcer ses propriétés mécaniques. Le cuivre contribue également à réduire le taux de croissance des IMC (Intermetallic Compound), ce qui peut être bénéfique pour la fiabilité à long terme.
- Nickel (Ni): Le nickel est utilisé pour améliorer les propriétés mécaniques de la soudure et pour stabiliser la couche intermétallique, réduisant ainsi la croissance de phases fragiles. Cela peut être particulièrement bénéfique dans les applications où les joints de soudure sont soumis à des contraintes mécaniques.
- Antimoine (Sb): L'antimoine peut être ajouté aux soudures Sn-Bi pour améliorer leurs propriétés thermiques et mécaniques. Il permet d'affiner la microstructure de la soudure, ce qui se traduit par de meilleures performances sous l'effet des cycles thermiques et des contraintes.
- Indium (In): L'indium peut augmenter la ductilité de la soudure, la rendant moins cassante. Cela peut être particulièrement utile dans les applications où la flexibilité et la résistance à la fatigue thermique sont importantes.
Chacun de ces éléments contribue de différentes manières aux performances globales de la soudure. Le choix du ou des éléments à ajouter dépend des exigences spécifiques de l'application, telles que l'environnement d'exploitation, les types de contraintes auxquelles les joints de soudure seront soumis et l'équilibre souhaité entre le coût et la performance. Les proportions de ces additifs doivent être soigneusement contrôlées, car des quantités excessives peuvent entraîner d'autres problèmes tels qu'une fragilité accrue ou une capacité de mouillage réduite.
Déterminer l'intérêt commercial du brasage à basse température aujourd'hui et à l'avenir
Déterminer le bien-fondé de la soudure à basse température (LT) implique d'évaluer les facteurs immédiats et à long terme de la fabrication électronique. Les considérations clés comprennent la comparaison des coûts entre les soudures LT et les soudures traditionnelles, la prise en compte des économies potentielles à long terme résultant de la réduction de la consommation d'énergie et la possibilité d'utiliser des composants moins chers. La compatibilité de la soudure à LT avec les lignes de fabrication existantes, ainsi que la nécessité de modifier l'équipement, constituent un élément essentiel de cette évaluation.
Il est essentiel de tenir compte des exigences spécifiques aux produits, en particulier pour les composants sensibles à la température, ainsi que de la fiabilité et des performances de la soudure à LT dans diverses conditions. En outre, les avantages environnementaux et la conformité réglementaire, en accord avec les tendances mondiales en matière de développement durable, jouent un rôle important dans cette évaluation.
Les perspectives d'avenir, telles que la tendance à la miniaturisation des appareils électroniques et l'évolution du marché vers des processus de fabrication plus respectueux de l'environnement, sont également importantes. L'analyse de rentabilité de la soudure LT repose donc sur un équilibre entre les besoins opérationnels immédiats, les avantages à long terme et l'adaptation à l'évolution des tendances de l'industrie et des demandes des consommateurs.
L'importance de la collaboration avec l'industrie
La voie à suivre exige un effort concerté en matière de recherche collaborative, combinant l'expertise du monde universitaire, de la fabrication et de la technologie de brasage pour explorer des domaines tels que la consommation d'énergie, les interactions entre les matériaux, etc. La mise en place de plateformes ouvertes pour le partage des connaissances, associée à des liens renforcés entre l'industrie et le monde universitaire, sera cruciale pour résoudre les problèmes non résolus et favoriser l'innovation. Cette approche collaborative promet de libérer tout le potentiel de la soudure à LT dans la fabrication électronique, en transformant les défis en tremplins pour l'avancement et l'efficacité dans ce domaine en pleine évolution.
CONCLUSION
Notre examen complet de la soudure à basse température (LT) dans l'assemblage et la retouche des composants électroniques a mis en évidence son rôle complexe dans la fabrication moderne. L'analyse comparative de diverses stratégies de reprise a révélé des différences nuancées en termes de qualité des joints, de croissance de l'IMC et de durée du processus, mettant en lumière les meilleures pratiques adaptées à des objectifs de fabrication spécifiques. En résumé, de meilleurs joints retravaillés ont été formés en utilisant des températures de pointe de fer plus élevées et des temps de contact modérés. En outre, nous avons pu confirmer que les résidus d'oxyde de bismuth résultant de la reprise ou de la refusion de soudures à basse température contenant du bismuth pouvaient être nettoyés si ces résidus posaient un problème.
En fin de compte, nous avons conclu que, bien que la brasure LT présente de nombreux avantages pour le brasage par refusion, il n'y a pas beaucoup d'arguments en faveur de l'utilisation de la brasure LT pour la reprise en raison de la complexité, du coût et de l'absence relative d'avantages par rapport à la reprise avec des SAC. En outre, jusqu'à ce que de nouvelles découvertes produisent des alliages LT plus fiables, nous constatons des inconvénients associés à la fragilité et aux défaillances dues aux chocs de chute qui doivent être mis en balance avec les économies d'énergie et de coûts du brasage à LT, ce qui fait que l'électronique consommable est peut-être le meilleur cas d'utilisation actuel.
À l'avenir, le développement et l'adoption plus large de la soudure à LT dépendront des défis à relever grâce à l'innovation collaborative, à la recherche continue et à l'adaptation aux nouvelles exigences de l'industrie. Le voyage à travers les subtilités de la soudure à LT suggère un chemin d'apprentissage et d'adaptation continus, où la collaboration industrielle peut tirer parti de son potentiel pour répondre aux demandes croissantes de la fabrication électronique.
RÉFÉRENCES
[1] Tang, K. K., Aspandiar, R. F., Mokler, S., Chen, O., & Jiang, A. (2015). SMT Soldering with Low Temperature Solder Paste. Intel Corporation.
[2] Mei, Zequn & Hua, Fay & Glazer, J. & Chung, C. Key. (1997). Low temperature soldering. Circuit World. 10. 463 - 476. 10.1109/IEMT.1997.626966.
[3] Intel. (2017). Introduction au soudage à basse température (LTS). Intel Corporation. Copyright 2017.
[4] Coyle, R., Anselm, M., Hadian, F., Kempaiah, S., Raj, A., Popowich, R., Clark, L., Fullerton, J., & Johnson, C. (2021, November 1). The Effect of Peak Reflow Temperature on Thermal Cycling Performance and Failure Mode of Hybrid Low Temperature Solder Joints (L'effet de la température de refusion maximale sur les performances de cyclage thermique et le mode de défaillance des joints de soudure hybrides à basse température). SMTA International 2021, 1er novembre 2021
[5] Dušek, K. & Bušek, David & Veselý, Petr & Pražanová, Anna & Plaček, Martin & Re, Julia. (2022). Comprendre l'effet du profil de refusion sur les propriétés métallurgiques des soudures étain-bismuth. Metals. 12. 121. 10.3390/met12010121.
[6] Sloan, M., Flanagan, K., Sandy-Smith, B., Allen, M. B. (2018). Profilage de refusion pour les alliages de soudure de nouvelle génération. Indium Corporation. Clinton, NY, USA.
[7] O'Neill, T., Fijalkowski, J., Tafoya, C., Xu, Y., Hrcek, S., Lambert, L., Willis, B., Hamasha, S. (Année). Addressing Low-Temperature Rework Concerns. AIM Solder. Montréal, Québec, Canada.
[8] Fu, Haley & Aspandiar, Raiyomand & Chen, Jimmy & Cheng, Shunfeng & Chen, Qin & Coyle, Richard & Feng, Sophia & Hardin, Bill & Krmpotich, Mark & Mokler, Scott & Radhakrishnan, Jagadeesh & Ribas, Morgana & Sandy-Smith, Brook & Tang, Kok & Wu, Greg & Zhang, Anny & Zhen, Wilson. (2018). Projet iNEMI sur le développement de processus de pâtes à braser à basse température à base de BISN - Partie II : Caractérisation des joints de soudure BGA en alliage mixte. 1-17. 10.23919/PanPacific.2018.8318989.
[9] iNEMI. (2019). Rapport sommaire de l'enquête iNEMI : Low Temperature Solder (LTS) Readiness for Volume Board Assembly. Publié en mai 2019.
AUTORISÉ PAR
Timothy O'Neill, Gayle Towell
AIM Solder
Cranston, Rhode Island, États-Unis
Elizabeth Norwood
MicroCare
New Britain, Connecticut, États-Unis
Hoa Nguyen
Metcal
Cypress, Californie, États-Unis
*PRESENTED AT IPC APEX 2024
REMERCIEMENTS
Les auteurs tiennent à remercier Yanci Gomez, technicien R&D de AIM Solder, et Itzayana Lopez, chimiste R&D de AIM Solder, pour leur aide dans l'analyse transversale.