In den letzten Jahren ist das Interesse der Elektronikhersteller an internen Recyclingsystemen für Lotkrätze wieder gestiegen. Die Aussicht auf eine Verringerung des Einkaufsvolumens von Lötstäben und des Abfalls von Lötkrätzen klingt zwar finanziell vorteilhaft, aber die Komplexität, die mit der Ausführung dieser Recyclingsysteme verbunden ist, wird oft unterschätzt. Diese Komplexität kann Hersteller dazu veranlassen, die Integration dieser Systeme zu überdenken oder sie nach der Implementierung aufgrund unvorhergesehener Herausforderungen und Ineffizienzen wieder aufzugeben.
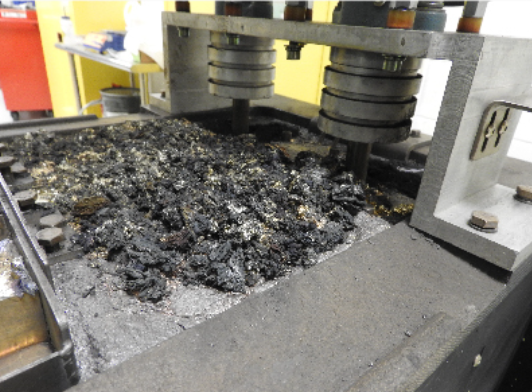
Integrität von Lötwellen und Kontaminationsrisiken
Innerbetriebliche Recyclingsysteme, wie sie für Lötkrätze verwendet werden, bergen das Risiko, dass höhere Mengen an Oxiden wieder in die Lötwelle eingebracht werden, wie in einem Papier mit dem Titel "In House Dross Recovery - Do You Know What You Are Putting Back in Your Solder Bath?" (Holtzer & Fullerton, 2015). Diese Rückführung ist auf das Fehlen eines umfassenden Aufbereitungsprozesses zurückzuführen, der in der Regel von professionellen Recyclern eingesetzt wird, und kann die Qualität der Verbindungen und die Zuverlässigkeit der Produkte beeinträchtigen.
Dieses Risiko wird noch durch die Möglichkeit einer Kreuzkontamination verstärkt, bei der sich Fremdmaterialien mit dem recycelten Lot vermischen können. Solche Verunreinigungen können zu erhöhten Kosten im Zusammenhang mit Nacharbeiten, Garantieansprüchen und in schwerwiegenden Fällen dazu führen, dass der gesamte Löttopf recycelt werden muss.
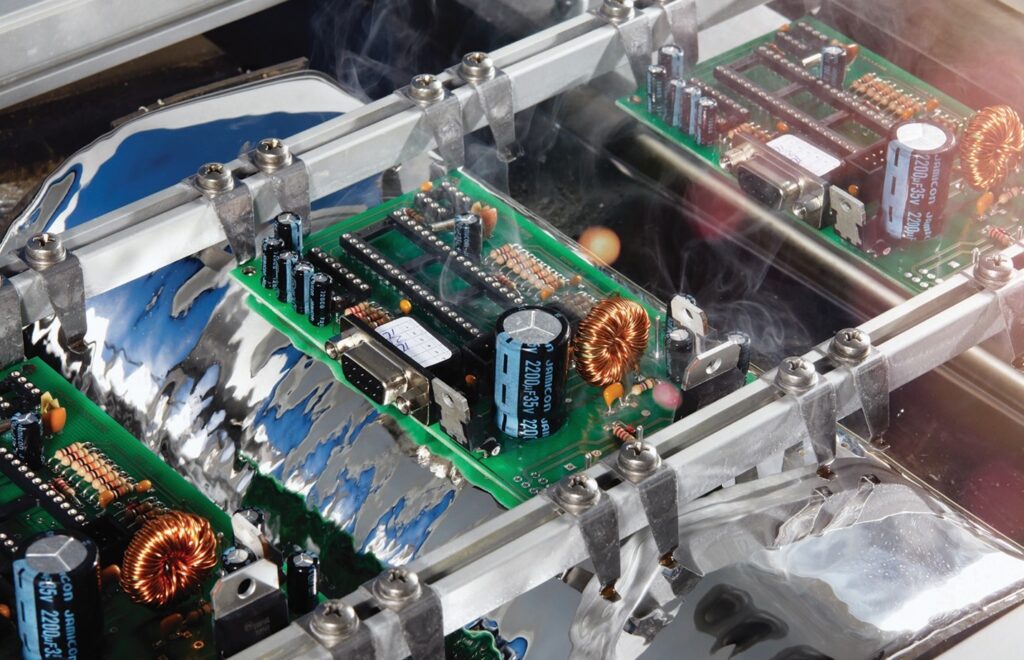
Ökologische und regulatorische Erwägungen
Die Auswirkungen auf die Umwelt und die behördlichen Auflagen für die Einrichtung interner Recyclingverfahren können erheblich und finanziell belastend sein. Elektronikhersteller unterliegen strengen Qualitätskontrollnormen und werden oft strengen Prüfungen unterzogen, um die Konsistenz und Zuverlässigkeit ihrer Produkte zu gewährleisten.
Die Einhaltung von Umweltvorschriften ist oft mit erheblichen anfänglichen und laufenden Investitionen verbunden. Um die Qualität des recycelten Lots zu überprüfen, sind genauere Prüfungen und Dokumentationen erforderlich, was die Produktion verlangsamen und den Verwaltungsaufwand erhöhen kann.
Darüber hinaus muss der Endabfall, der hauptsächlich aus Oxiden besteht, aus denen kein weiteres Lot gewonnen werden kann, ordnungsgemäß gehandhabt und entsorgt werden, was in der Regel die Rückgabe an Lieferanten erfordert, die für eine effiziente und sichere Entsorgung solcher Abfälle ausgerüstet sind.
Qualitätssicherung und Risiken bei der Legierungszusammensetzung
Das firmeninterne Recyclingverfahren erschwert die Standardqualitätsprüfungen aufgrund von Schwankungen in der Legierungszusammensetzung zusätzlich. Dies wird in der Veröffentlichung von Holtzer & Fullerton deutlich, in der festgestellt wird, dass sich die Elementverhältnisse der recycelten Legierungen ändern können (z. B. Zinn zu Silber und Zinn zu Blei), was zu unvorhersehbaren Legierungseigenschaften und potenziellen Ausfällen bei Anwendungen mit hoher Zuverlässigkeit führt.
Platzbeschränkungen und betriebliche Effizienz
Der Platz in den Produktionsanlagen ist ein kritisches Gut, das oft direkt mit der Produktionskapazität und -effizienz verbunden ist. Der für interne Recyclingsysteme benötigte Platz kann zu erheblichen Opportunitätskosten führen. Der für die Recycling-Anlagen vorgesehene Platz könnte ansonsten für zusätzliche Produktionslinien oder andere umsatzfördernde Aktivitäten genutzt werden. Dieser Kompromiss muss sorgfältig abgewogen werden, insbesondere in Einrichtungen, in denen der Platz knapp ist.
Aus betrieblicher Sicht kann das innerbetriebliche Recycling den Fokus von den Kernaktivitäten der Produktion ablenken. Die Schulung und das laufende Management des Recyclingprozesses erfordern spezielle Fähigkeiten, die den betrieblichen Aufwand erhöhen. Es stellt sich auch die strategische Frage, ob die Hersteller wollen, dass sich ihre Ingenieure auf das Recycling oder auf die Kernproduktion und Innovation konzentrieren.
Sicherheits- und Gesundheitsaspekte des Bedieners
Die Kosten für die Bereitstellung und Wartung von Sicherheitsausrüstungen und die Einhaltung von Gesundheits- und Sicherheitsvorschriften machen den Einsatz von Recyclingsystemen noch komplexer und teurer.
Der Umgang mit Lötkrätzen und der Betrieb von Recyclinganlagen ist mit der Exposition gegenüber potenziell schädlichen Stoffen und zweifellos mit dem Umgang mit geschmolzenen Metallen verbunden. Um die Sicherheit des Personals zu gewährleisten, sind angemessene Schutzmaßnahmen, Schulungen und möglicherweise ein erhöhter Versicherungs- und Haftungsschutz erforderlich.
Wirtschaftliche Erwägungen und verminderter Rückgewinnungswert
Interne Recyclingsysteme können zwar den Bedarf an neuem Lot verringern, wirken sich aber auch in mehrfacher Hinsicht auf die Wirtschaftlichkeit der Lotverwendung aus. So muss beispielsweise der Prozess des Abschöpfens und der Trennung von Metall und Krätze sorgfältig gesteuert werden, um zu vermeiden, dass mehr Metall als Krätze verarbeitet wird, was fälschlicherweise als verbesserte Leistung der Maschine erscheinen kann.
Diese wirtschaftliche Auswirkung kommt zu den bereits erwähnten zusätzlichen Kosten hinzu, wie z. B. Versorgungsleistungen, Arbeitskräfte für den Betrieb der Recyclinganlagen und komplexere Anforderungen an die Abfallentsorgung. Außerdem sinkt der Rückgewinnungswert des endgültigen Abfallmaterials, da es einen viel geringeren Prozentsatz an metallischen Bestandteilen und eine höhere Konzentration an Verunreinigungen und Oxiden aufweist.
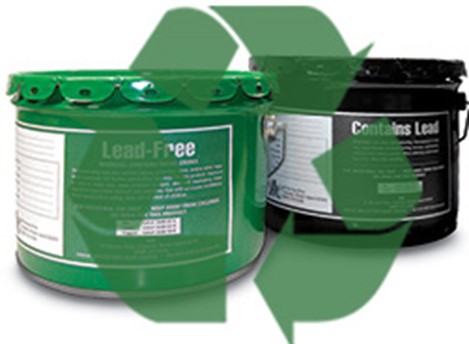
Eine einfachere und oft effizientere Alternative besteht darin, die Rückgewinnung der Krätze den Lotherstellern zu überlassen. Auf diese Weise können die Unternehmen den Rückgewinnungswert für das Material erhalten, ohne sich um die Komplexität, die versteckten Kosten und die potenzielle Haftung im Zusammenhang mit dem internen Recycling kümmern zu müssen. Dieser Ansatz stellt nicht nur sicher, dass die professionellen Standards für das Recycling eingehalten werden, sondern ermöglicht es den Elektronikherstellern auch, sich auf ihr Kerngeschäft zu konzentrieren, ohne die zusätzliche Belastung durch die Verwaltung von Recyclingmaßnahmen.
Schlussfolgerung
Das innerbetriebliche Recycling von Lötkrätzen mag zwar eine attraktive Möglichkeit für Kosteneinsparungen und Umweltverantwortung darstellen, doch die zahlreichen Herausforderungen und versteckten Kosten, die damit verbunden sind, dürfen nicht übersehen werden. Die Komplexität, die mit der Aufrechterhaltung der Legierungsintegrität, der Einhaltung von Umweltauflagen, der Verwaltung der betrieblichen Effizienz und dem Schutz der Gesundheit der Mitarbeiter verbunden ist, stellt ein erhebliches Hindernis dar. Die Hersteller müssen diese Faktoren sorgfältig gegen die wahrgenommenen Vorteile abwägen, um zu entscheiden, ob das interne Recycling mit ihren betrieblichen Zielen und Qualitätsstandards vereinbar ist.
Referenzen
Holtzer, M., & Fullerton, J. (2015). In House Dross Recovery - Do You Know What You Are Putting Back in Your Solder Bath? Proceedings of SMTA International, September 27 - October 1, 2015, Rosemont, IL.